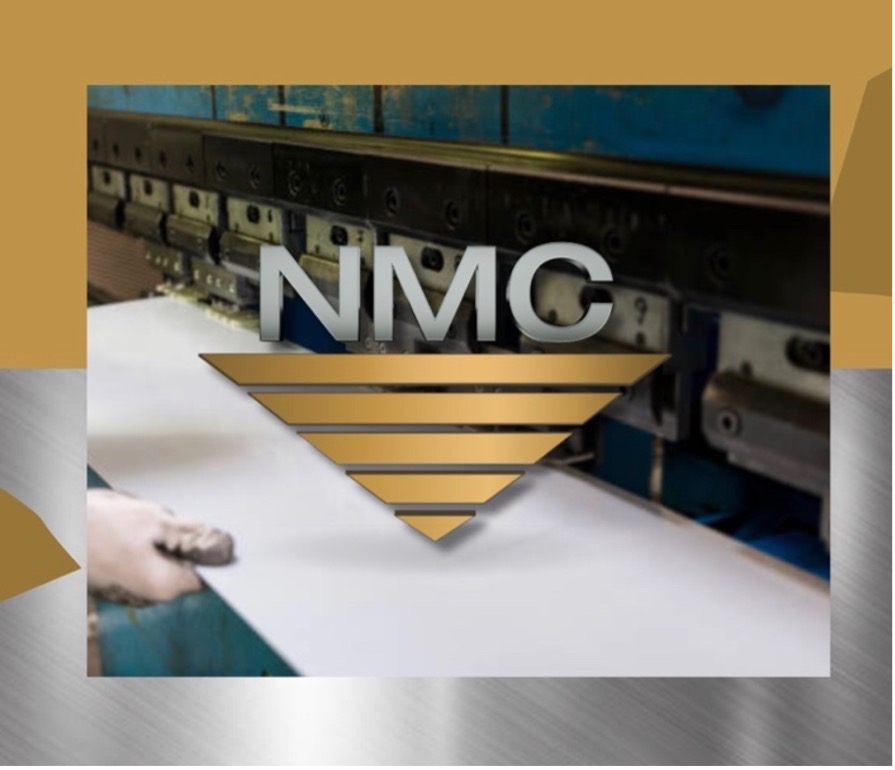
National Material Company is regarded as a global leader in servicing the needs of the steel industry and leading industrial and consumer product manufacturers. With over 50 years of expertise in metals processing and supply chain management, NMC offers metal stamping services as a part of a wide array of steel processing capabilities. Read on to learn more about metal stamping:
Metal Stamping Process
Metal stamping is an incredibly versatile and efficient manufacturing process that takes flat metal sheets or coils and transforms them into precisely shaped and intricate parts. By utilizing force, pressure, and specialized tooling, components with diverse forms — including bends, curves, cutouts, and embossing, are possible. This process offers low costs and higher lead times — both for short and long production runs while keeping consistent quality, dimensional accuracy, and repeatability of the manufactured parts.
How It Works
At the core of metal stamping lies the stamp press, a component responsible for applying the necessary force and pressure to mold the metal sheets or coils into the desired shape or profiles. This powerful machine incorporates specialized tooling known as dies, which performs a variety of stamping operations on the metal. By carefully controlling the movement of the press and the interaction between the dies and the metal in the production line, the stamping process brings forth remarkable transformations in the shape and structure of the material.
Now, let’s dive deeper into the fascinating world of metal stamping and explore its different stages and intricacies.
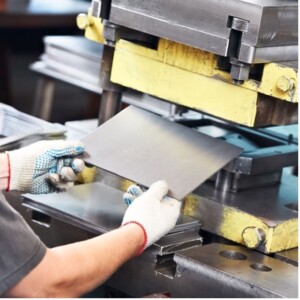
Design and Tooling Preparation
Experts begin the process with meticulous design and engineering, where the desired part geometry is carefully planned. Stamping professionals consider multiple factors such as material properties, die design, and tooling requirements. Once the design is finalized, it is plotted using CAD (computer-aided design) or CAM (computer-aided manufacturing) software to ensure accuracy. After the tool design is completed, the specialized tooling (such as blanking dies, forming dies, and piercing dies), is fabricated using a variety of machining tools and technology. The tool and die design must ensure proper material flow, adequate clearance for the metal sheet, and appropriate support for the part during stamping.
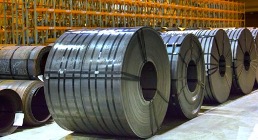
Material Preparation
Based on the requirements of the part, specialists select metal sheets or coils. Considerations include mechanical properties such as strength and ductility, as well as other factors like corrosion resistance, conductivity, and cost. The selected material should be compatible with the stamping process and the desired part’s functionality.
Feeding
The selected materials undergo preparation processes like cutting, slitting, and leveling to obtain the proper dimensions and flatness necessary for stamping. The prepared metal sheets or coils are then fed into the stamping press, where an automated feeding mechanism ensures precise positioning for accurate stamping.
Stamping Operations
As the stamp press initiates its action, the dies close together, subjecting the metal to high force and pressure. This pressure deforms the material, shaping it according to the contours of the dies. There are also a variety of metal-forming processes that may be involved in stamping. These include blanking (cutting out the desired shape), bending (creating angles or curves), coining (adding fine details), and punching (making holes or cutouts), which these experts perform sequentially or simultaneously, depending on the part design.
Throughout the stamping process, operators implement quality control measures, including real-time monitoring and inspections. They ensure that the parts meet the specified tolerances and quality standards.
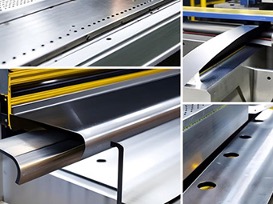
Finishing and Post-Processing
After stamping, these professionals may apply additional post-processing steps, such as deburring (removing sharp edges), cleaning, surface treatment, and coating, to enhance the appearance, durability, and functionality of the stamped parts.
By following this systematic approach, the stamping process transforms raw metal sheets or coils into precisely shaped components that serve diverse industries and applications. It is an exciting blend of precision engineering, material science, and advanced manufacturing techniques that continue to revolutionize the way we produce complex metal parts.
Metal stamping can be categorized into several types based on the specific techniques and processes involved. Here are some common types of stamping:
Progressive Stamping
a high-volume production process that utilizes a series of dies arranged in a progressive manner. The metal sheet or coil is continuously fed through the dies, and each station performs a specific operation, such as cutting, bending, or forming. It allows for the creation of complex parts with multiple features in a single pass.
Transfer Stamping
Similar to progressive stamping, but instead of the metal sheet moving continuously through the dies, mechanical systems transfer the sheet from one station to another. Companies use this method often for larger and more complex parts that may require additional operations or precise positioning.
Four-Slide Stamping
Also known as multi-slide stamping, this is a specialized technique that uses a four-slide machine to form intricate shapes or perform multiple bending and forming operations simultaneously. Operations commonly use multi-slide stamping for small, complex parts with multiple bends or curves.
Deep Drawing
A stamping process used to create cylindrical or box-shaped parts with significant depth. A specialist will place a blank over a die and which is then forced into the die cavity using a punch. As the metal undergoes plastic deformation, it takes the shape of the die cavity, resulting in a deep-drawn component.
Fine Blanking
A precision stamping process used to produce high-quality, burr-free parts. It involves the use of a specialized fine blanking die that incorporates three distinct cutting edges. When components that require exceptional flatness, dimensional accuracy, and edge quality, specialists will often use fine blanking.
These are some of the primary types of stamping processes. Each type has its own advantages and applications, and manufacturers select the most appropriate method based on factors such as the complexity of the part, required production volume, and desired quality.
Types of Stamping Presses and Dies
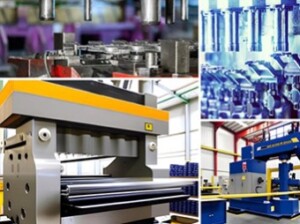
- Mechanical presses are the most widely used type of stamping presses. It utilizes motor power — usually provided by a flywheel, to apply force to the metal sheet. Mechanical presses offer high speed and are suitable for high-volume production. They can be further classified based on their drive mechanisms, such as crank, eccentric, or knuckle-joint presses.
- Hydraulic presses use hydraulic power to generate force. This press employs hydraulic cylinders to exert pressure on the metal sheet, allowing for precise control and adjustment. Hydraulic presses are known for their high-force capabilities and suitability for heavy-duty operations and often used for deep drawing.
- Servo presses combine the advantages of mechanical and hydraulic presses with the precision of servo motor control. They use a servo motor to control the slide movement, enabling highly accurate positioning, speed control, and programmability. Servo presses are preferred for applications that require precise control, flexibility, and energy efficiency.
How Metal Stamping is Applied
Metal stamping finds widespread applications across various industries due to its versatility and ability to produce high-quality, precisely shaped, and unique components.
-
Automotive Industry
It plays a vital role in the automotive manufacturing industry — producing components such as body panels, brackets, chassis parts, engine mounts, brackets, and suspension components. The process ensures the production of lightweight, durable, and structurally sound parts that meet stringent safety and performance requirements.
-
Aerospace Sector
Metal stamping also reached the heavens through the aerospace sector. Key components like aircraft structural parts, engine parts, brackets, and fittings can be fabricated with the process which ensures the production of lightweight parts with complex geometries while maintaining strength and durability, contributing to enhanced fuel efficiency and performance.
-
Electronics Industry
In the electronics industry, electronic devices (connectors, terminals, heat sinks, shielding components, and brackets) are widely used. Metal stamping made it possible for the precise fabrication of intricate parts required for electronic assemblies while ensuring proper electrical conductivity and durability.
-
Household Appliances
The process is also employed extensively in the manufacturing of household appliances like refrigerators, washing machines, ovens, and HVAC systems. It produces components such as panels, enclosures, brackets, and handles, providing both aesthetic appeal and structural integrity.
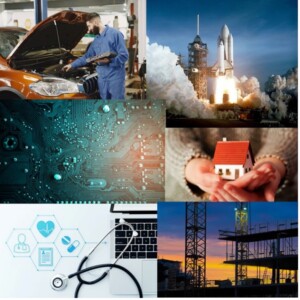
-
Healthcare Industry
In the medical field, devices such as surgical instruments, orthopedic implants, brackets, and connectors also have components that have undergone the metal stamping process ensuring the production of precise, sterile, and biocompatible parts critical for medical applications.
-
Construction Industry
And how can we forget the construction industry, where metal stamping products are present in structural and decorative components like brackets, connectors, fasteners, hinges, and cladding panels — to name a few? Overall, the process allows the creation of durable, corrosion-resistant parts that meet the demanding requirements of the industry.
Metal stamping is an intricate process that demands the expertise and proficiency of a company well-versed in the field. When your industry requires the best metal stamping products and services, National Material Company (NMC) is the obvious choice. Renowned as a leading metal processor, NMC excels at providing exceptional solutions to meet your exact standards.
NMC offers a diverse range of capabilities, including metal stamping, by leveraging technological breakthroughs and innovations developed over years of compelling research and development. We’ve worked with diverse industries and delivered superior products and services across the globe, and in working with us, we guarantee…
ISO Certified Quality System
Computer-controlled, High-speed Precision Shearing and Blanking
Sheets and Plates capabilities
Precision Slitting capabilities
Pickling Stamping and Pre-notching Capabilities
Complete Metallurgical Lab and Testing Facilities
About National Material Company
National Material Company prides ourselves in being an industry leader in the metal stamping market by providing cost and time-effective solutions with steel service centers across the United States, Mexico, and Canada. NMC is a well-recognized global leader servicing the needs of the steel industry and leading industrial and consumer product manufacturers. With over 50 years of expertise, we’d love to realize your vision with our wide array of capabilities.
NMC is part of the National Material Limited Partnership (NMLP) steel division, which is one of the largest independent steel service centers in the United States. NMLP operates 16 steel service centers and processing facilities in the United States, Canada, and Mexico and ships over 2,000,000 tons of steel annually.
Please contact us at nationalmaterial.com, email us at nmcquotes@nmlp.com, or call (U.S.) 847-806-7200 to discuss how we can be of service.